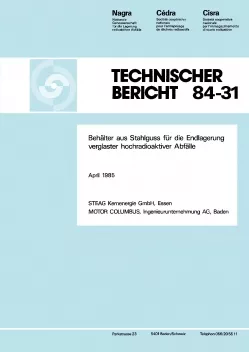
Technischer Bericht NTB 84-31
Behälter aus Stahlguss für die Endlagerung verglaster hochradioaktiver Abfälle
The present concept of Nagra for the disposal of highly active, vitrified waste from reprocessing in the crystalline bedrock of Northern Switzerland includes containers as one of several safety barriers. Such containers are required to remain leaktight and withstand an external isostatic pressure of 300 bar (corresponding to the maximum swelling pressure of the compacted bentonite used as buffer material).
The report describes a container made of cast steel GS 40 designed for the above requirements: the container consists of a thick-walled, self-supporting cylindrical shell with hemispherical ends, one of these being a lid that is welded onto the main body of the container. The external diameter is 940 mm and the total length 2'000 mm. The wall thickness is 250 rnm in the cylindrical body and 150 mm in the hemispherical ends. On the inside of the lower part of the container and of the lid extra radiation shields are provided. The total weight of the container filled with vitrified HLW is 8'900 kg. The container is constructed so that, under the external pressure of 300 bar, tensile or shear stresses that might be detrimental from the point of view of corrosion are avoided or kept to very low levels. Particular attention was devoted to ensuring the absence of stresses at the weld by designing carefully the welding surfaces and the contact surface between lid and body of the container; the weld's only purpose is to ensure leaktightness. The processes necessary for the manufacture and quality assurance are state-of-the-art.
The required long-term corrosion resistance is obtained through the provision of a 50 mm corrosion allowance; this is conservative since the results of the corrosion programme of Nagra indicate that a maximum depth of penetration of less than 30 mm in 1'000 years is to be expected.
Due to its appreciable wall thickness the container ensures a sufficient shielding of the radiation emitted by the waste, so that direct handling by operating personnel is possible. The maximum dose rate at the surface of the cylinder is 100 mrem/h (1 msv/h); at the surface of the bottom and the lid, only 30 mrem/h (0.30 mSv/h); the dose originates mainly from neutrons. The good shielding properties of the container also keep the gas generation from radiolysis low. For instance, the hydrogen yield calculated using conservative assumptions is not more than 30 mg in 1'000 years; this is negligible compared to the hydrogen generation from the corrosion of iron, which amounts to 44 kg in 1'000 years.
The stress and stability analyses carried out assuming a corroded container with a wall thickness reduced by 50 mm show that under the design external isostatic pressure of 300 bar the highest stress is less than 80 N/mm2; this leads to a higher safety margin against yield than that required by the ASME code (ASME VIII, Division 1). The stability analysis carried out using the same code also shows high safety margins.
Calculations have furthermore been carried out under the very conservative assumption that the container has corroded on only one side. It was shown that, even in this case, failure will not take place. Finally, the long-term mechanical behaviour of the container, and particularly its creep behaviour have been investigated. It was concluded that at the design temperature and pressure creep failure of a container made of cast steel GS 40 can at worst occur after a significantly longer period of time than 1'000 years.