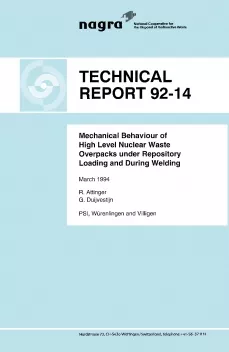
Technical Report NTB 92-14
Mechanical Behaviour of High Level Nuclear Waste Overpacks under Repository Loading and During Welding
One of the concepts for final disposal of high level nuclear waste in Switzerland consists of a mined repository approximately 1200 m deep in the crystalline bedrock of Northern Switzerland. In order to delay the return of the radionuclides to the biosphere, and to reduce their concentration there to acceptable levels, reliance is placed in the multiple safety barrier principle. In addition to the natural barriers (host rock and overlying sediments), the following engineered barriers are envisaged: the waste form itself (vitrified high level nuclear waste), an overpack, the purpose of which is to ensure isolation of the radionuclides from groundwater for a period of at least 1000 years, and a compacted bentonite backfill within which the overpack is placed horizontally in the axis of the repository gallery. This backfill is aimed at reducing the transport of water and dissolved species from the waste to the host rock.
The first part of the present work reports on the participation in the COMPAS project (COntainer Mechanical Performance ASsessment). This project was carried out within the framework of the European Atomic Energy Community's cost-sharing programme on 'Radioactive Waste Management and Disposal'. It was concerned with the mechanical performance of overpacks for vitrified high level nuclear waste. First, the COMPAS project was intended to demonstrate that overpacks can be designed which will be able to withstand the loadings anticipated in deep geological repositories. Second, it investigated the current analytical capability with regard to the prediction of the behaviour of overpacks under both anticipated repository loads and extreme loading conditions. There has been a strong emphasis on predictive finite element calculations in the COMPAS project, with experimental test work to provide data to check the calculations, through a series of models ranging from simple rings to realistic scale models, one in the form of the overpack from Nagra. One of our aims in the COMPAS project was to verify the finite element code used with experiments which are relevant to the design of overpacks.
The second part of this work deals with the issue of stress corrosion cracking of the high level nuclear waste overpack from Nagra which is made out of GS-40 cast steel. The design work carried out for the overpack (Steag & Motor-Columbus 1984) showed for the stresses a safety, margin of a factor 5 against the tensile strength. The issue of stress corrosion cracking must be raised whenever large tensile stresses are expected, even when a low strength steel with potentially good resistance to this type of corrosion is used. A project was initiated by Nagra in order to deal with this issue, the aims being to assess:
- the stress corrosion behaviour of the reference steel in a more detailed manner than in the earlier projects and including laboratory testing,
- the possibilities for modelling welding stresses and their full or partial relief using 'state-of-the-art' computer codes and
- the feasibility of achieving adequate relief of the welding stresses.
The above-mentioned aim (2) is the subject of the second part of this work. After a description of the material properties of GS-40 cast steel, the one-dimensional FIBRE model is discussed, which should give an insight into the parameters involved in a thermomechanical calculation of a welding process. Next the thermomechanical calculation for the evaluation of residual stresses using the finite element method is described; it includes the calculation procedure and the verification of the proposed user-supplied material model for the simulation of the material behaviour at high temperature and during multipass welding and stress relief.
The calculations were performed with the commercially available finite element code ADINA (ADINA 1984). The output from ADINA was used as input to the postprocessor ORVIRT (Bass & Bryson 1983) when fracture calculations are considered. During the simulation of the welding process, the need for a user-supplied material model for the simulation of material behaviour at high temperature became obvious. This was implemented in the finite element code SOLVIA (SOLVIA 1987) which was derived from ADINA version 84.
The work presented allows concluding the following:
- The commercially available finite element code ADINA is suitable for the stress analysis of high level nuclear waste overpacks under repository loading and during welding.
- It was demonstrated that the behaviour of an overpack can be modelled to a level of accuracy within engineering limits with the help of the finite element code ADINA. The verification and validation work performed in the COMPAS project treated creep, fracture mechanics problems and buckling; the experiments were simulated by two-dimensional or three-dimensional models considering elastoplastic material behaviour and large displacements. The material model used to simulate the material behaviour at high temperature was verified with an experiment where two annuli are welded together by means of electro-beam welding.
- The assumptions used in the thermomechanical calculations for the simulation of the welding process are important for the residual shape of the work piece, but not for the residual stresses. The calculated residual stresses are high and, therefore, they are limited by the yield limit. The calculated tensile stresses around the weld may reach the yield limit.
- The stress relief obtained in a post-weld heat treatment may be maintained during the subsequent cooling to ambient temperature when the cooling process is performed appropriately. Rapid cooling may result in large residual stresses which will not be reduced in all cases, even if viscous effects are considered.